When discussing the safety and efficiency of lifting operations, LOLER training plays a pivotal role. LOLER regulations is crucial for anyone involved in operating or managing lifting equipment, which spans a broad range of machinery and accessories, from construction hoists to cranes, and even includes personal lifting accessories like safety harnesses.
Understanding LOLER is not only about adhering to legal requirements; it’s also about ensuring the utmost safety in workplaces where lifting equipment is used. LOLER training equips individuals with the necessary knowledge to inspect and operate lifting equipment safely, reducing the risk of accidents and enhancing overall workplace safety.
LOLER applies to a variety of sectors, including construction, warehousing, and maritime operations. Any business or individual involved in lifting operations should be aware of these regulations. This blog will delve into the specifics of the different types of equipment covered under LOLER, highlighting how proper training and compliance can lead to safer, more efficient work environments.
LOLER training is not just for those directly handling the lifting equipment; it’s also essential for managers and supervisors. They need to understand the regulations to ensure their teams are compliant and that safety procedures are strictly followed. This comprehensive approach to safety can significantly reduce workplace incidents and increase productivity.
Loler training and critical elements of LOLER
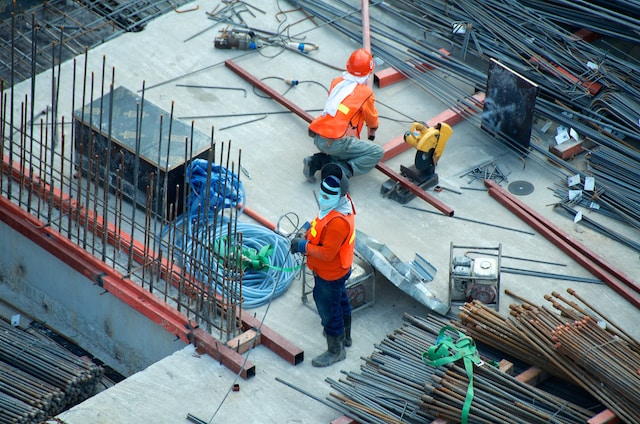
All lifting equipment must be thoroughly examined by a competent person and records must be kept.
All equipment owners or managers (known as duty holders) must abide by LOLER. This includes employers, self-employed people, and anyone renting work equipment.
LOLER offers comprehensive lifting equipment insurance solutions, including accessories such as karabiners, slings, chains, and cabling systems.
This table provides a comprehensive overview of the critical elements of LOLER that the blog can expand upon in detail.
Aspect | Details |
---|---|
Regulation Name | Lifting Operations and Lifting Equipment Regulations 1998 (LOLER) |
Scope of Equipment | Cranes, forklifts, hoists, work platforms, lifts, and safety harnesses |
Training Relevance | Safe operation of lifting equipment, Routine inspections, Identification of hazards |
Sectors Affected | Construction, Warehousing, Maritime, Manufacturing, and Transportation |
Key Objectives | Ensuring safety in lifting operations, Compliance with legal standards, Risk reduction |
Responsibilities | Equipment maintenance, regular inspections, reporting defects, Adequate training provision |
Frequency of Inspections | Varies based on equipment type and usage. Typically ranges from 6 to 12 months. |
Documentation | Record of inspections, maintenance logs, and training records |
Legal Penalties | Fines, Legal action for non-compliance, Suspension of operations |
Benefits of compliance | Increased safety, Reduced accident risk, improved operational efficiency |
Lifting devices
Lifting operations involve lifting loads that can be heavy and hazardous, necessitating careful planning to minimise accidents. Accidents involving lifting equipment may have serious repercussions for its users and put their health or lives in jeopardy. Regulations aim to mitigate such risks by placing duties and responsibilities on those who own, operate, or control lifting equipment.
LOLER regulations were developed as an expansion of PUWER (Provision and Use of Work Equipment Regulations). They cover any device that may be used to lift loads, including equipment intended to anchor, support, or fix them, such as cranes, forklift trucks, lifts, and hoists (mobile elevating work platforms with hoists as well as vehicle inspection platform hoists), plus any accessories like chains or slings that might be used for these purposes.
Owners, operators, or individuals with control of equipment must take responsibility for ensuring its safe use by having it examined periodically by a competent person. This individual must be capable of determining the scope of the examination based on practical knowledge and training, as well as recommendations in any pertinent codes of practice or guidance documents.
Before any new equipment is put into service, after repairs or replacement of essential components, and at intervals recommended by its manufacturer, more frequent inspections may also be necessary if there is evidence of high risk.
Competent persons must also conduct pre-use checks on equipment before each use to ensure its safety and detect defects before they become a serious issue. These may involve simple visual or functional tests; however, more extensive assessments may be necessary for some types of equipment.
Some equipment is exempt from LOLER coverage, such as customer lifts in shopping centres because they don’t serve any work-related purposes and dentist chairs because of their low risk. But this doesn’t absolve them of maintenance requirements, and they may need periodic PUWER inspections for safety checks.
Lifting accessories
Load lifting equipment comes in many forms, from lifts and forklift trucks to cranes and mobile elevating and vehicle inspection platforms. It includes anything that can lift, lower, or anchor loads; this may also include attachments used to anchor, fix, or support them, such as hoists, lifting slings, and chains. Though these do not necessarily need LOLER inspections (the Provision and Use of Work Equipment Regulations would cover that), they still must be safe and suitable for the task at hand.
As an employer, self-employed individual, or anyone else responsible for operating lifting equipment, it is your duty to ensure its safe use by workers. One effective method for doing this is arranging regular statutory ‘thorough examinations’ by qualified personnel who use both practical and theoretical knowledge to inspect the machinery and detect any issues.
Inspection frequency depends on the type and use of equipment; in general, inspections should take place at least annually for most pieces. However, if exposed to conditions that could compromise its safety, such as outdoor storage for long periods, inspections may need to occur more frequently.
An equipment inspection must take place prior to use for the first time, following movement between locations, and at each new site where it will be used for the first time. Furthermore, repairs or any events likely to impact its safety, such as damage, failure, long periods out of service and major modifications, should also be thoroughly analysed.
As well as scheduling these exhaustive examinations, it is your duty to keep all relevant records relating to the equipment under review; this includes inspection reports, test certificates, and any EC Declarations of Conformity documents, which must always be readily available for inspections.
Mobile elevating and vehicle inspection platforms
LOLER training is essential to safe lifting operations for crane operators, engineering surveyors, building site workers, and warehouse operators of all kinds. The regulations cover an expansive array of equipment used for lifting, lowering, carrying, or supporting loads, such as mobile elevating platforms and vehicle inspection platforms, as well as cranes; safety-critical lifting accessories like chains and slings, mechanical hitches, prussiks, fimbl savers, and karabiners may also fall within their purview.
LOLER regulations cover employers, self-employed persons, and companies that own or control equipment that can be lifted or lowered, regardless of its source (e.g., a loan from another organisation or a rental). Any lifting operations should be planned out beforehand and managed safely to remain compliant. LOLER puts an obligation on those managing such equipment to ensure every lifting operation meets these criteria and operates safely.
It is imperative that each time you lift, a risk assessment be conducted and reviewed regularly. Furthermore, it must be ensured that a competent individual inspects equipment prior to every use so any defects that could compromise safety can be identified and assessed appropriately before lifting begins.
Regulations outline that a competent person is defined as someone with both practical and theoretical knowledge of lifting equipment as well as enough experience to detect defects or weaknesses. They must also remain impartial when conducting their inspection so as to provide an objective evaluation of its condition.
Regulations require that competent persons conduct a comprehensive six-monthly inspection of all equipment before it is used again, keeping and displaying a report with all the information. Papertrail makes this task effortless by creating reports with all required details that can easily be saved against each item and reproduced at any time as PDF printouts or digital displays.
Cranes
Equipment that must be checked to comply with LOLER includes everything from lifts and forklift trucks to cranes with runways, hoists, and their accessories, such as lifting slings and hoists, as well as their safe working load (SWL) marking. Furthermore, regulations stipulate that equipment be installed so as to minimise its chances of striking someone or inflicting injury on someone.
There are certain pieces of equipment that appear to be lifting equipment but are actually exempt from LOLER because they provide continuous transport of people or goods rather than lifting from one place to another. Examples include continuous types of lifts like escalators, stair lifts, and platform lifts used in hospitals, as well as hospital-specific versions; nevertheless, they must still be regularly inspected according to HSE’s general requirements and those set out in the Provision and Use of Work Equipment Regulations (PUWER).
Everyone responsible for selecting and operating work equipment must comply with LOLER regulations, regardless of whether they are an employer, a self-employed person, or someone renting equipment out. This includes safety managers, warehouse operatives, construction workers, and crane operators, in addition to engineers, surveyors, and health and safety advisors.
An LOLER training course provides the chance to gain more knowledge of lifting equipment laws as well as how to inspect equipment safely for safety. It is an essential piece of education for health and safety professionals looking to enhance their understanding of lifting regulations.
At LOLER inspections, it is essential that qualified individuals conduct them. These could include employers, owners, or employees responsible for equipment, provided that they possess sufficient knowledge and experience required by regulations to complete an exhaustive examination of it all. In some instances, this could mean hiring professional engineers or surveyors; on other pieces of equipment, a health and safety technician might be appointed instead.
For a guide on tarmac road surfacing contractors, check out our other guide in the Crosby Marina Club blog.